Components of an intumescent paint coating system
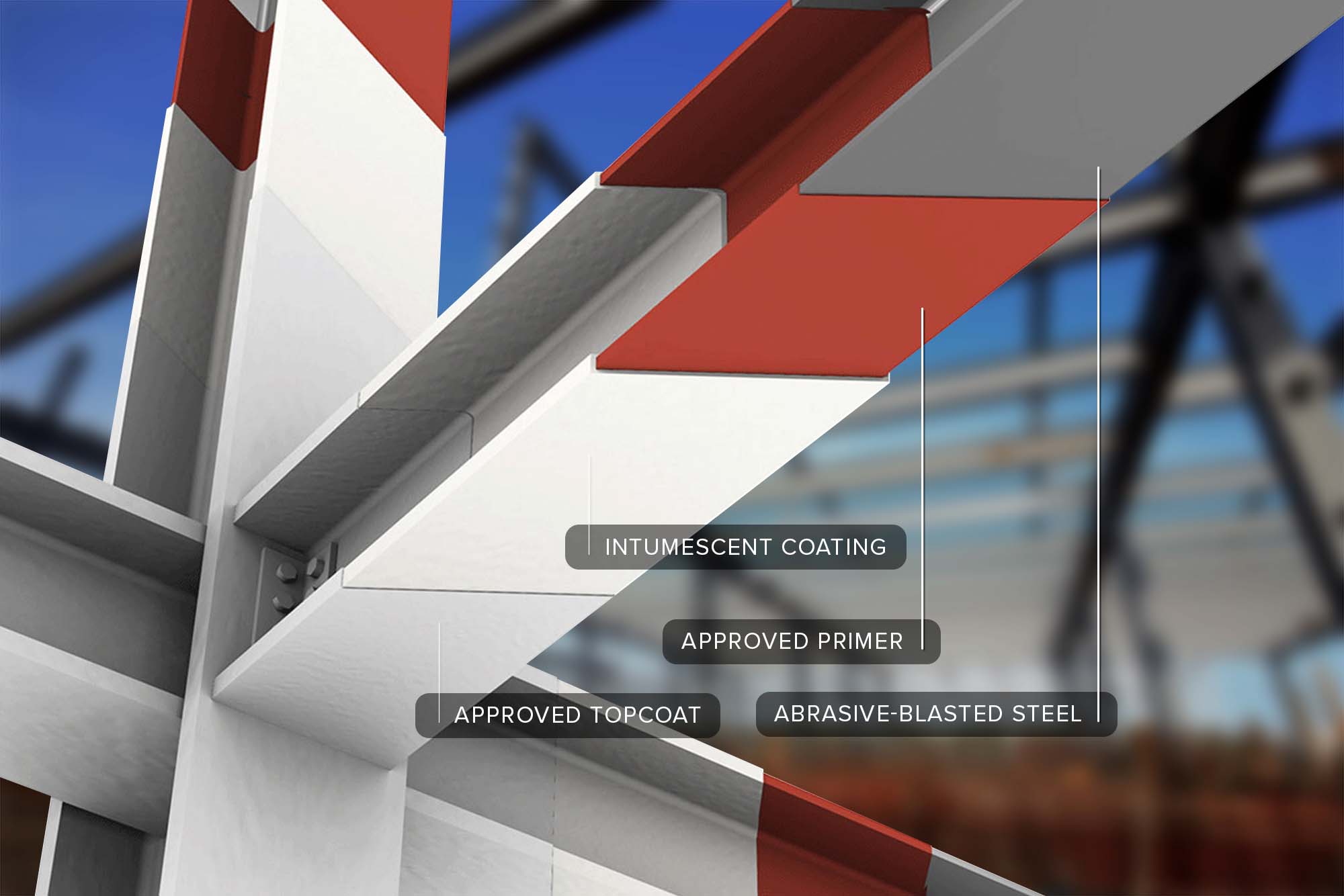
Intumescent paint coating systems generally have three components:
- A primer
- The intumescent coating or basecoat
- A sealer or topcoat
Of these three it is the basecoat that is the most important (in terms of passive fire protection)... this is the component that reacts to a fire.
Intumescent paint coating anatomy
This photo above shows the recommended coatings over mild steel. Consult with the intumescent paint coating manufacturer for their approved primer and topcoat... these vary from product to product.
All surfaces should receive an abrasive blast to SA2.5 prior to applying the approved primer.
Always refer to the relevant technical datasheet prior to use to ensure a product is suitable for your application.
Visit the manufacturer's website to find the relevant datasheet or check our own library of datasheets that are regularly udated.
The primer
The primary purpose of the primer is to assist with the adhesion of the basecoat to the steel. It should be applied in strict accordance to the manufacturer's data sheet in order to function correctly. Primer coats generally have a dry film thickness (DFT) of between 75 and 100 microns.
The dry film thickness of the primer should be measured to ensure compliance with the specification. This thickness should also be subtracted from the subsequent basecoat thickness in order to accurately assess the basecoat thickness.
Newer products such as Nullifire SC902 and Interchar 3120 for internal steel applications can go over blasted steel that has tightly adhered rust with no primer.
Note: this is only for internal structural steel elements within the enclosed building elements.
The basecoat - the intumescent coating itself
As already mentioned, the basecoat is the component that does all the heavy lifting.
It achieves its protective properies through these components:
- A catalyst, which decomposes to produce a mineral acid like phosphoric acid. A common catalyst is ammonium polyphosphate.
- A carbohydrate which combines with the mineral acid to form a carbonaceous char. Starch is a typical carbohydrate used.
- A binder (or resin) which softens at a predermined temperature within the upper limits of the reaction temerature range.
- A spumific agent which, together with the melting of the binder, decomposes to liberate large volumes of non-flammable gases. These gases include carbon dioxide, ammonia and water vapour. The production of these gases cause the binder to foam and expand, providing an insulating char many times the thickness of the original coating.
Basecoat wet film thickness (WFT) and dry film thickness (DFT) is determined by product loading schedules that take into account the steel section factor (Hp/A).
The topcoat (or sealer)
The primary purpose of the sealer is to protect against degredation of the basecoat. Thick film intumescent coatings may also need a sealer to prevent chalinking in situtions where the structure is exposed to ultraviolet or moist conditions.
Sealers also perform a decorative function in some applications. Various levels of finish can be applied depending on aesthetic requirements and budget.
In some instances, however, a sealer may not be necessary.
Download the PDF
click hereMore articles...
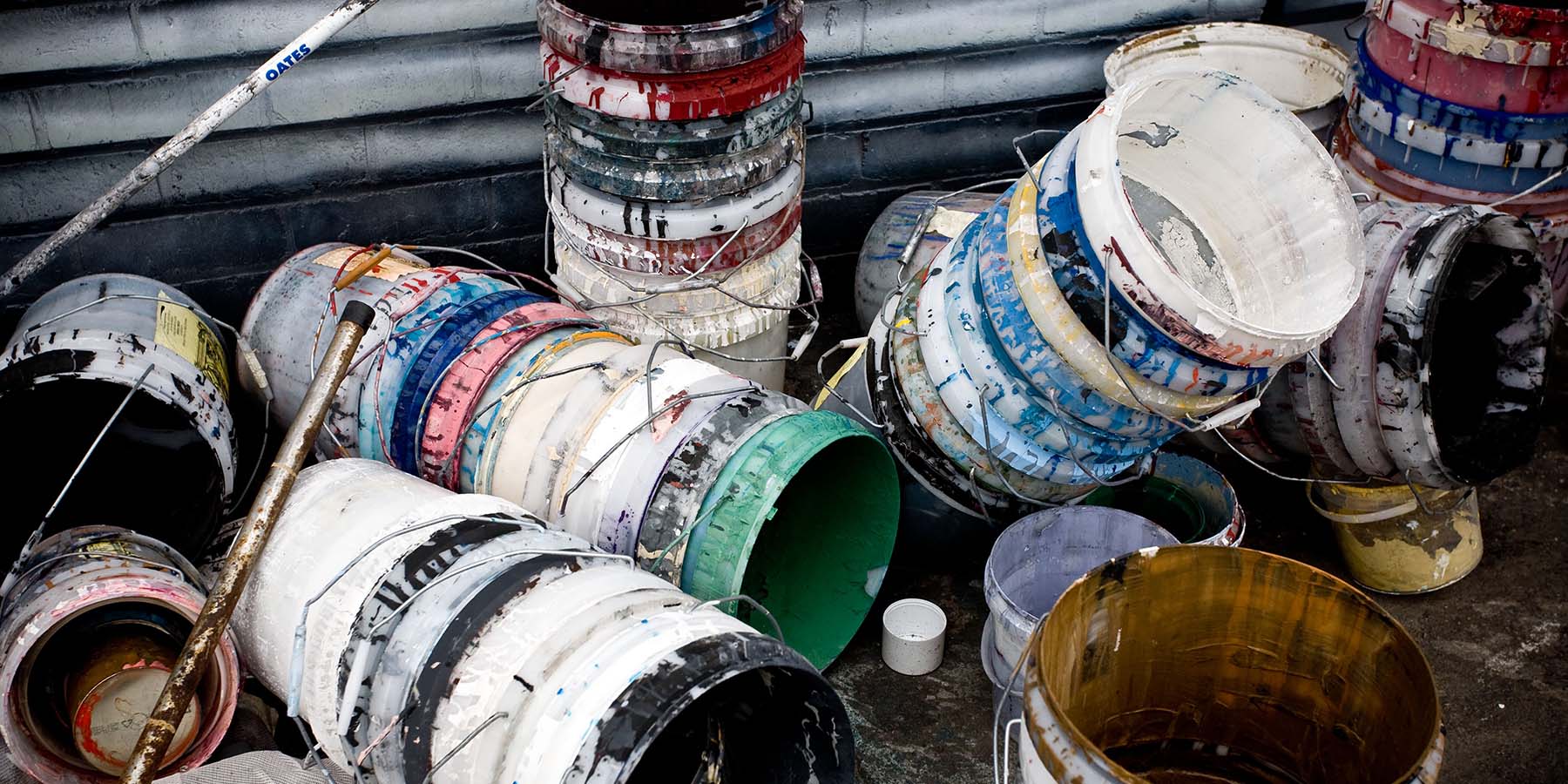
Intumescent coating types
There are a variety of intumescent coating types with different properties and application methods. Which type is the best for your situation?
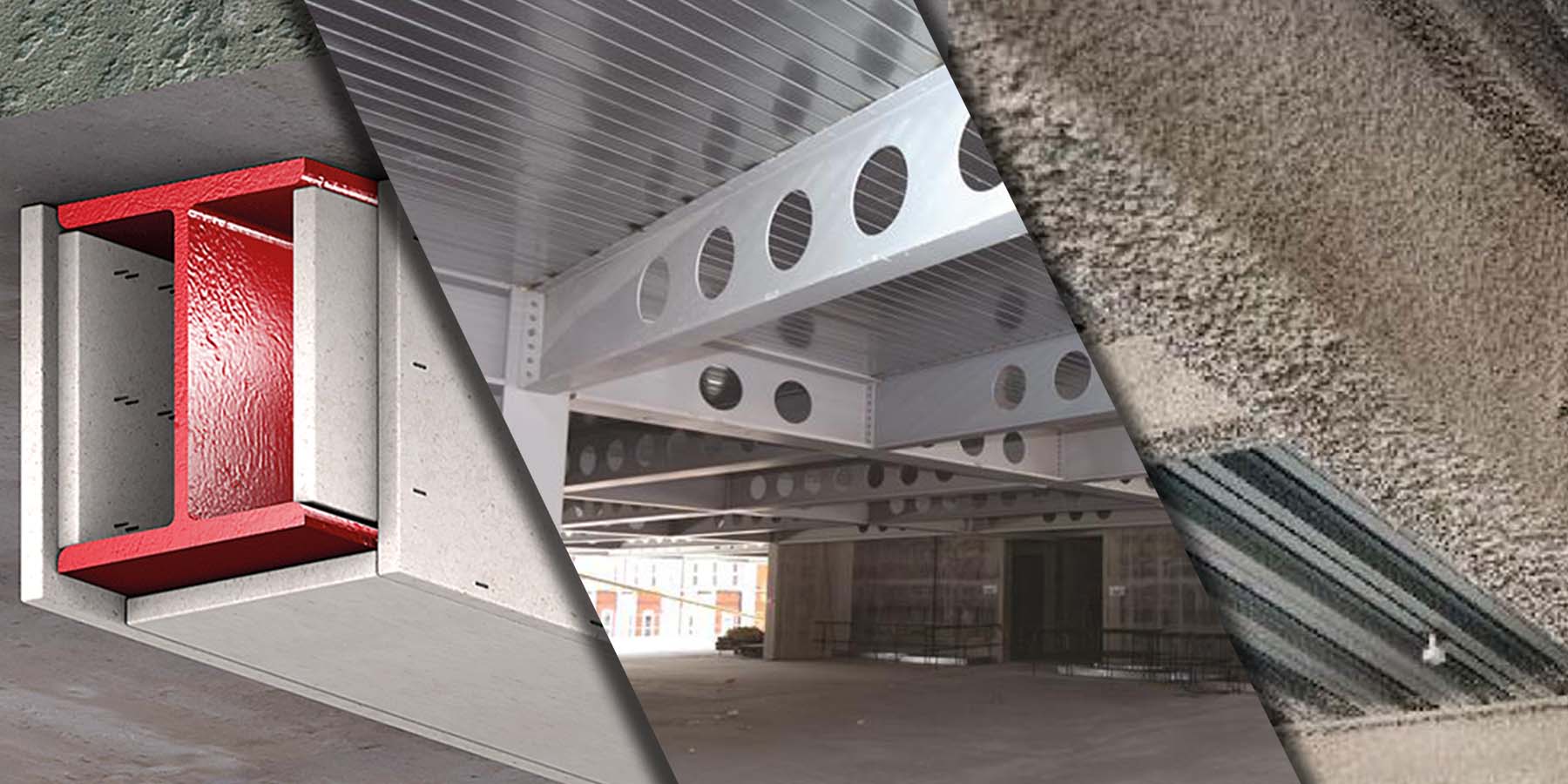
Passive fire protection methods
There are several ways to protect building structural work. Whilst some methods may be more prevalent, there is no one "best way" to protect a building's structure. The best method will most likely be determined by a number of factors, but here are your options.
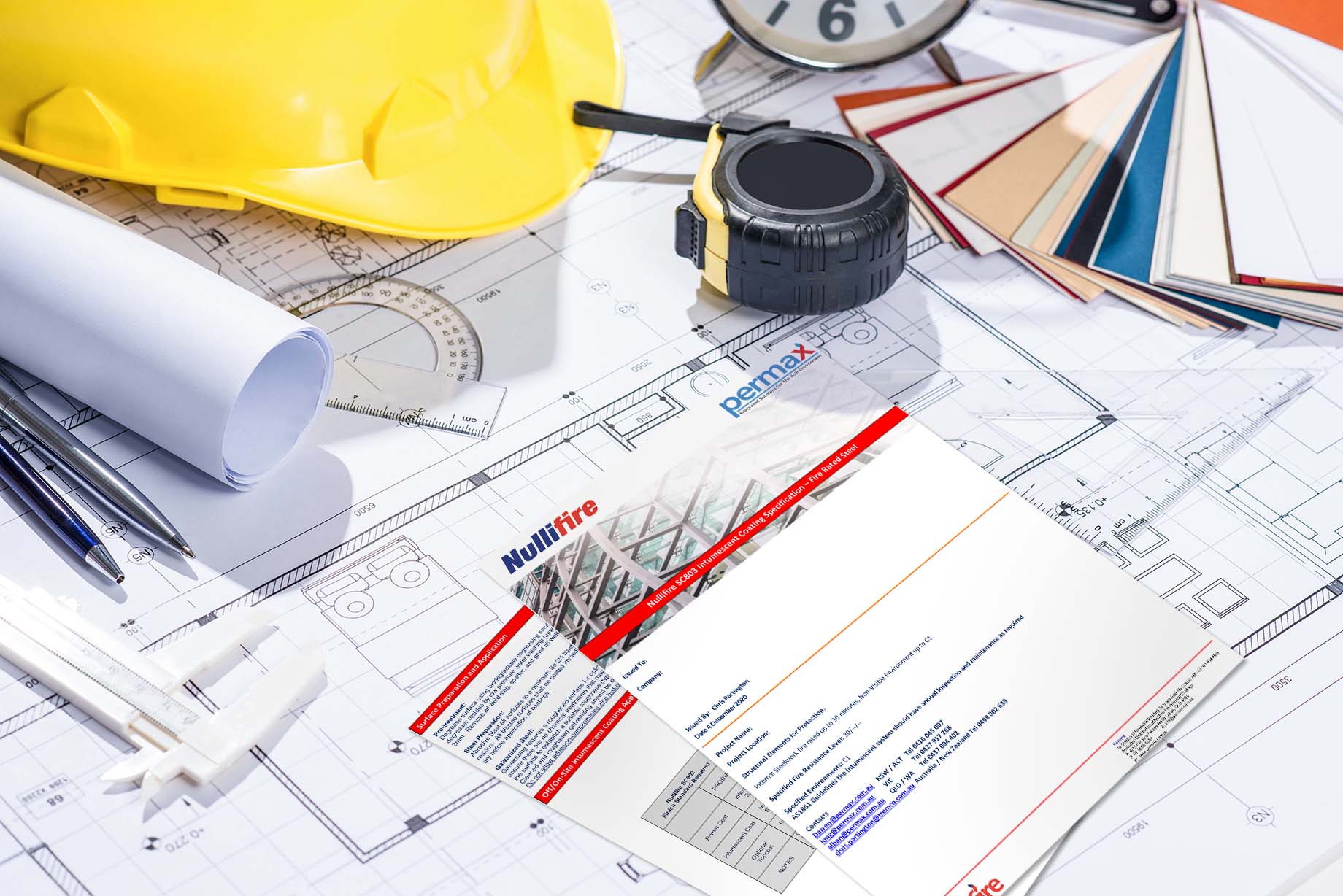
Intumescent paint coating specification templates
Access a range of templates supplied by manufacturers for the purposes of specifying their intumescent paint coating products for various FRLs and corrosivity ratings.
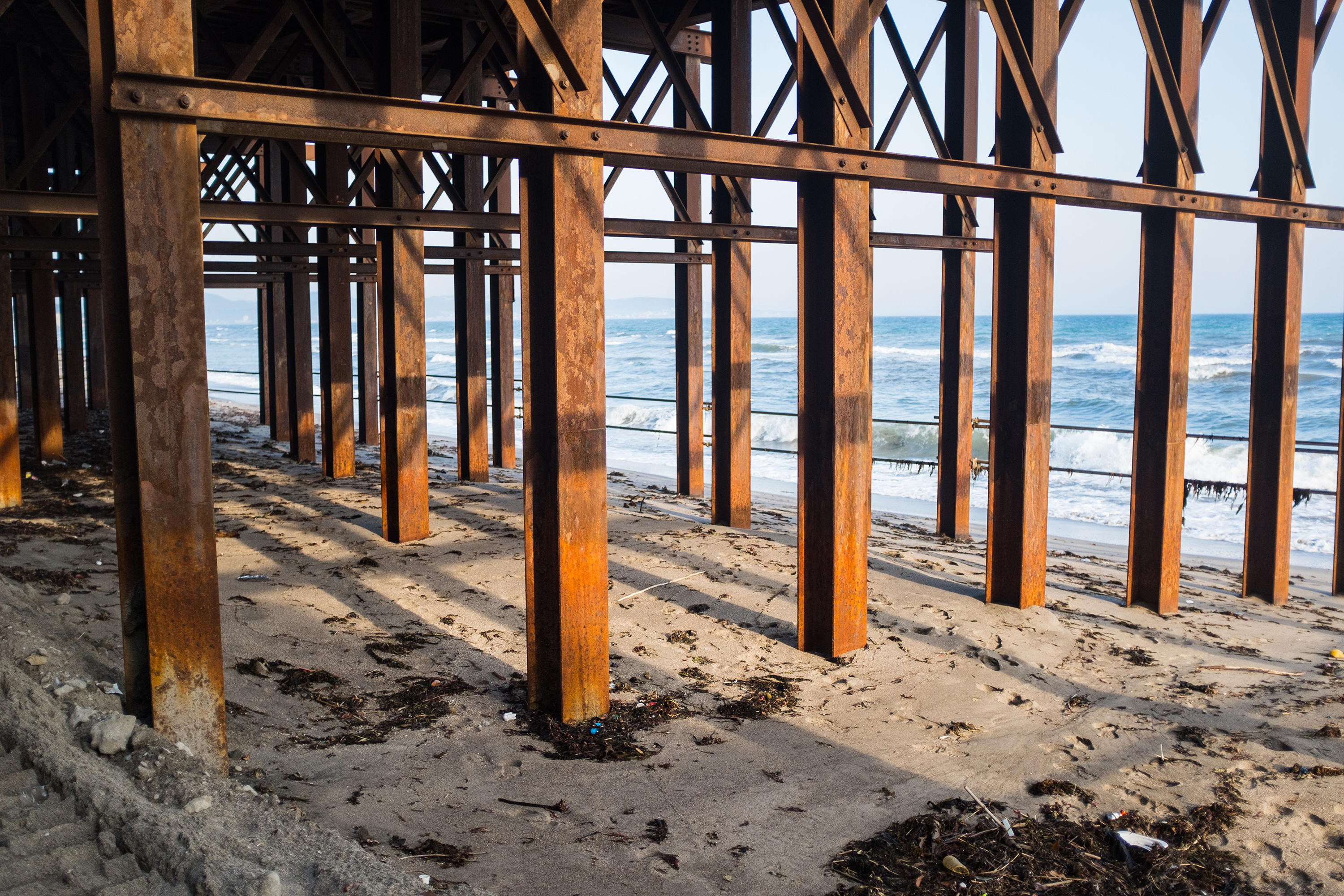
Intumescent paint coating corrosivity ratings in the Australian atmosphere
It's common knowledge that corrosion rates are affected by environmental factors, but do you know the various corrosivity ratings and their definitions?
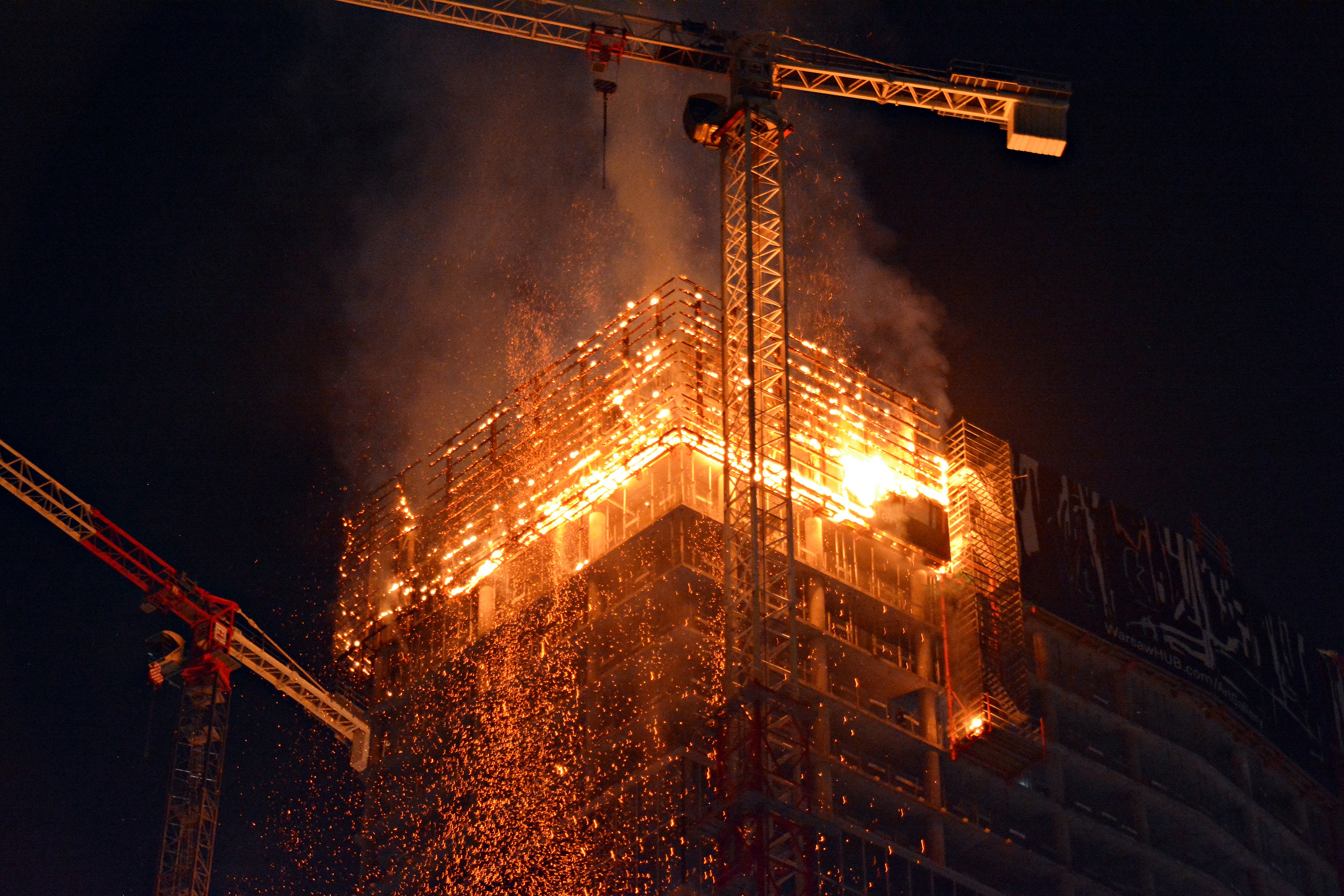
Limiting steel temperatures to maintain structural integrity
Maintaining structural adequacy on load-bearing steel is critical to the fire safety of building occupants, fire fighters and the surrounding built environment. Here's how limiting steel temperatures to maintain structural integrity relates to intumescent paint coatings.
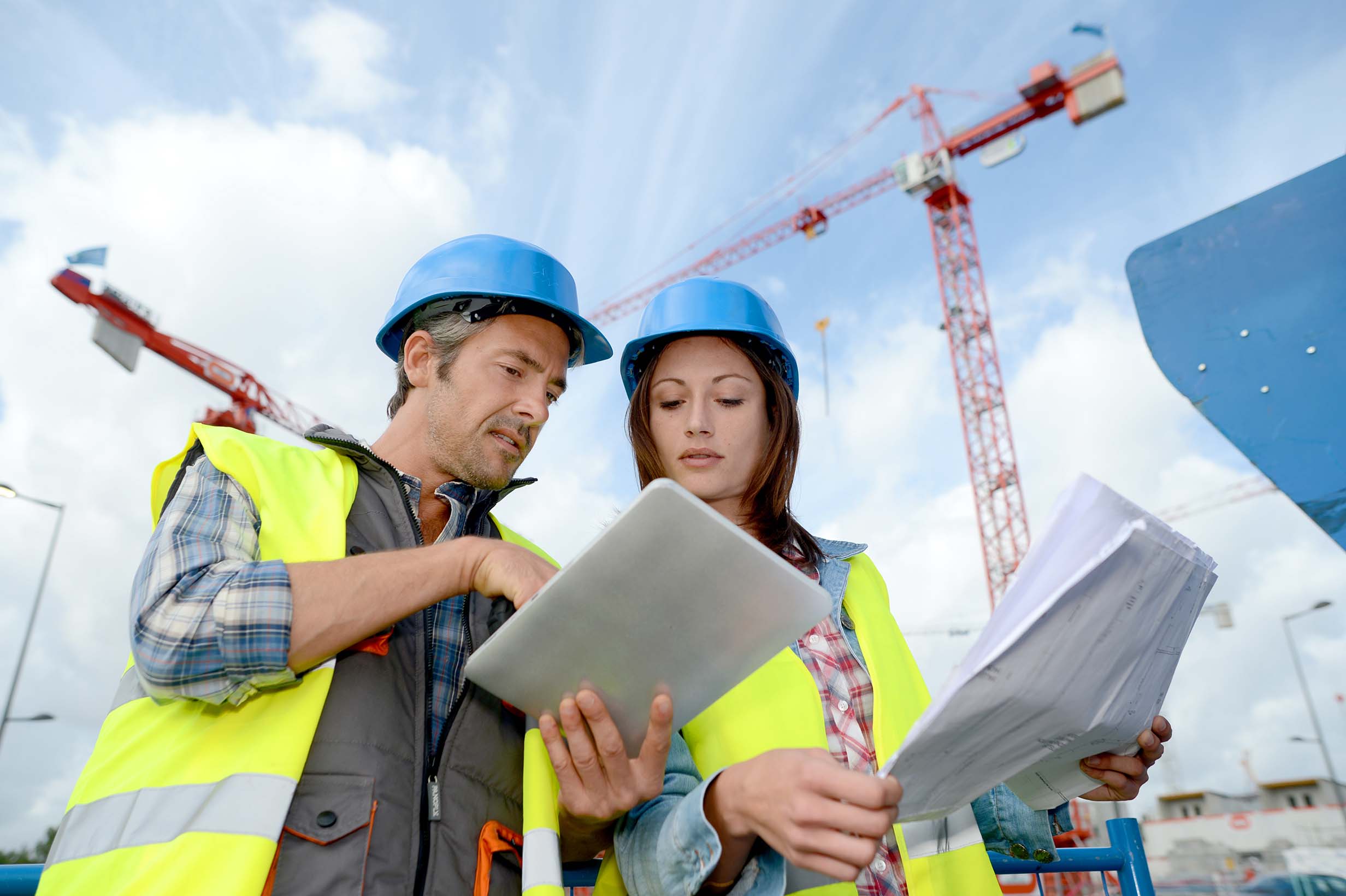
Getting help with intumescent paint coatings
The specifying and application of an intumescent coating system is a highly specialised task that requires considerable training and experience to accomplish correctly.
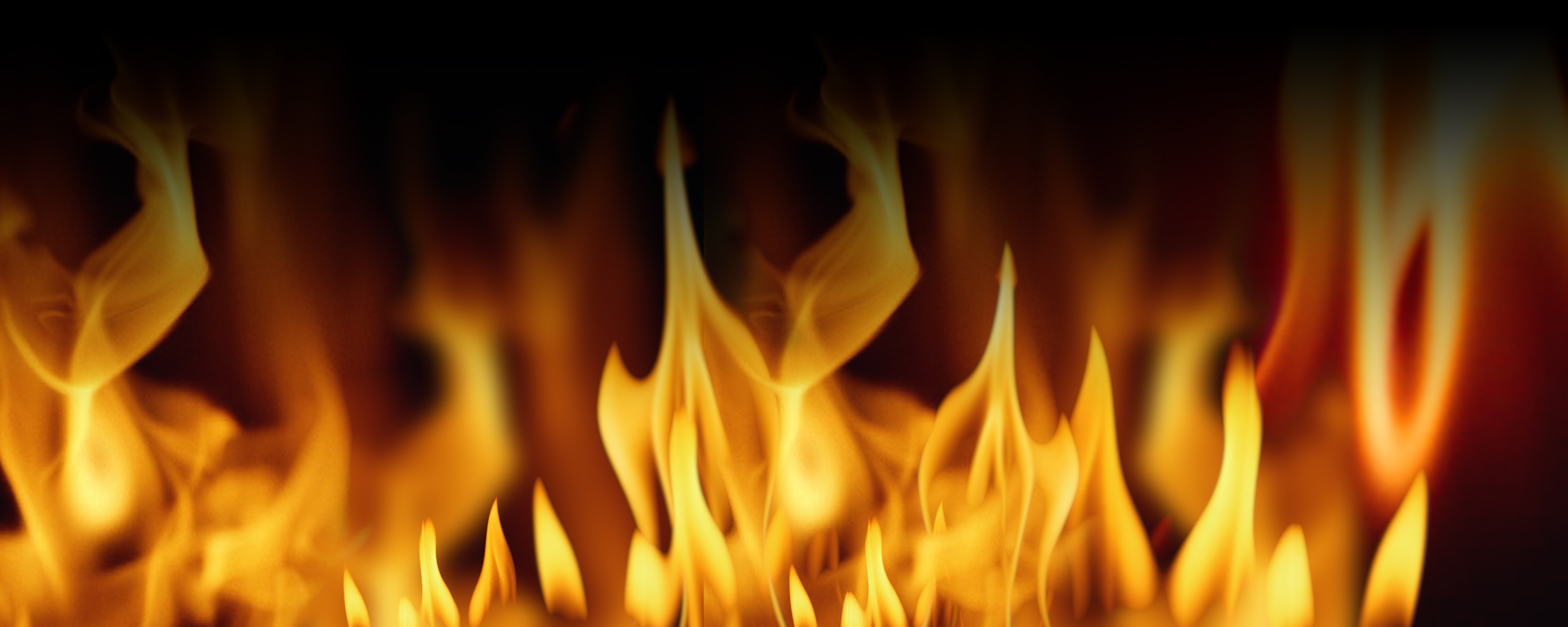
Fire types and severity
Different combustible materials burn at different temperatures which will have a bearing on the FRL of a given intumescent paint coating. This needs to be taken into account when specifying intumescent products so that the required FRL is ensured for the combustible materials that are likely to be encountered in a particular situation.
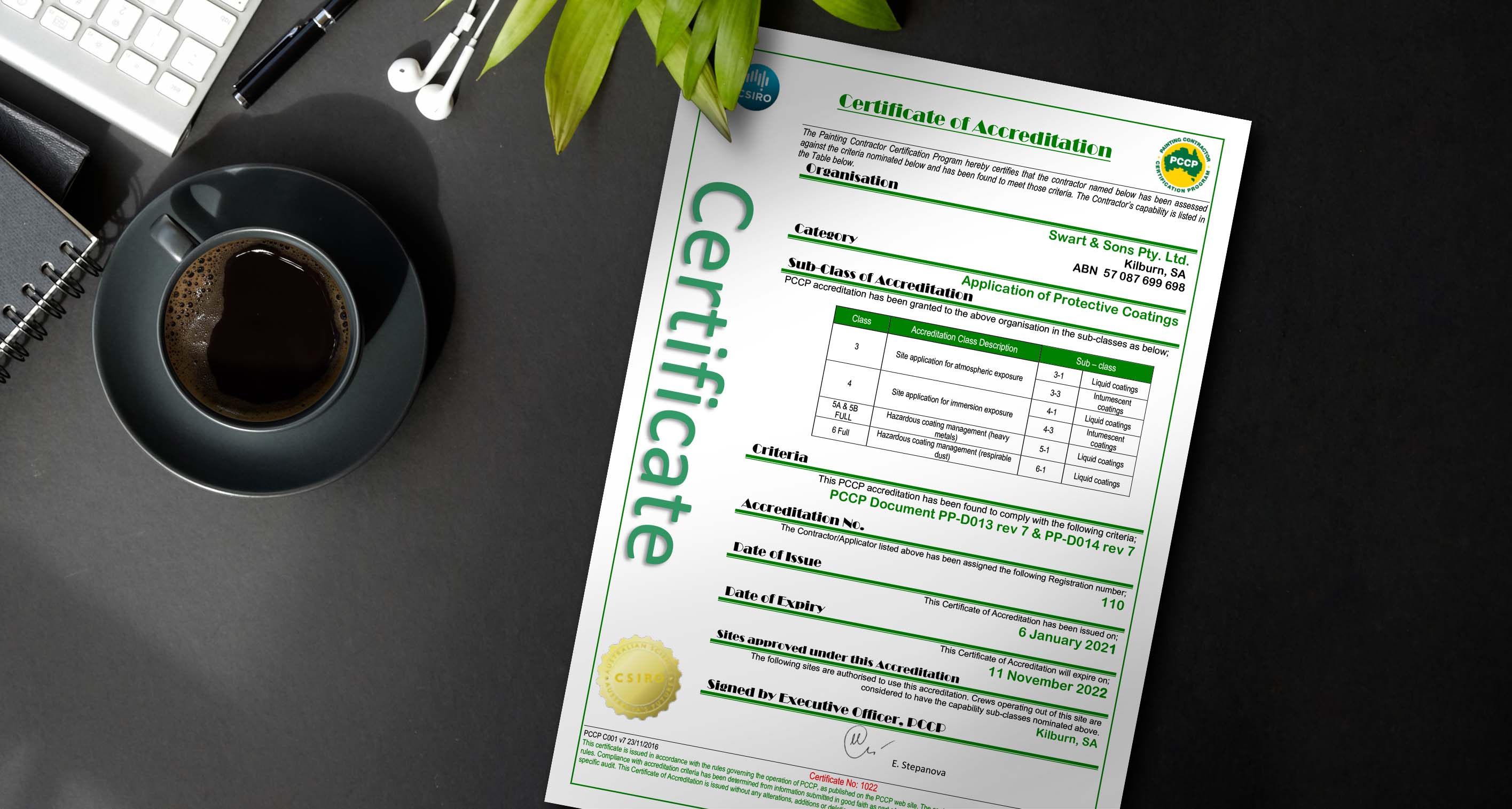
Quality assurance for intumescent paint coatings
We believe Painting Contractor Certification Program (PCCP) accreditation is paramount for passive fire protection contractors engaged in applying intumescent paint coating systems.
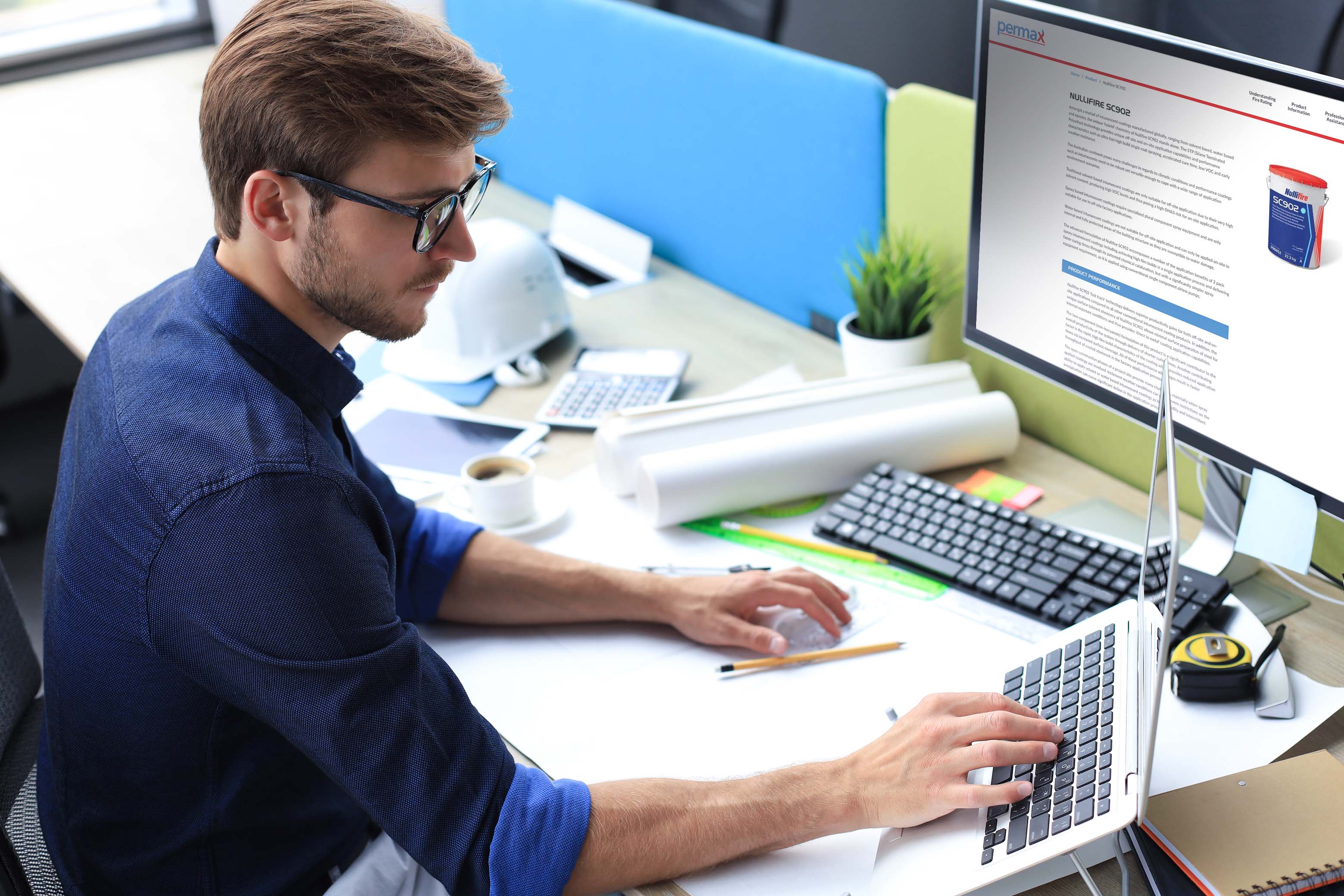
Specifying intumescent paint coatings
Whilst intumescent coating products may look just like paint, they have an important function (i.e. passive fire protection) that makes their specification a much more involved process.
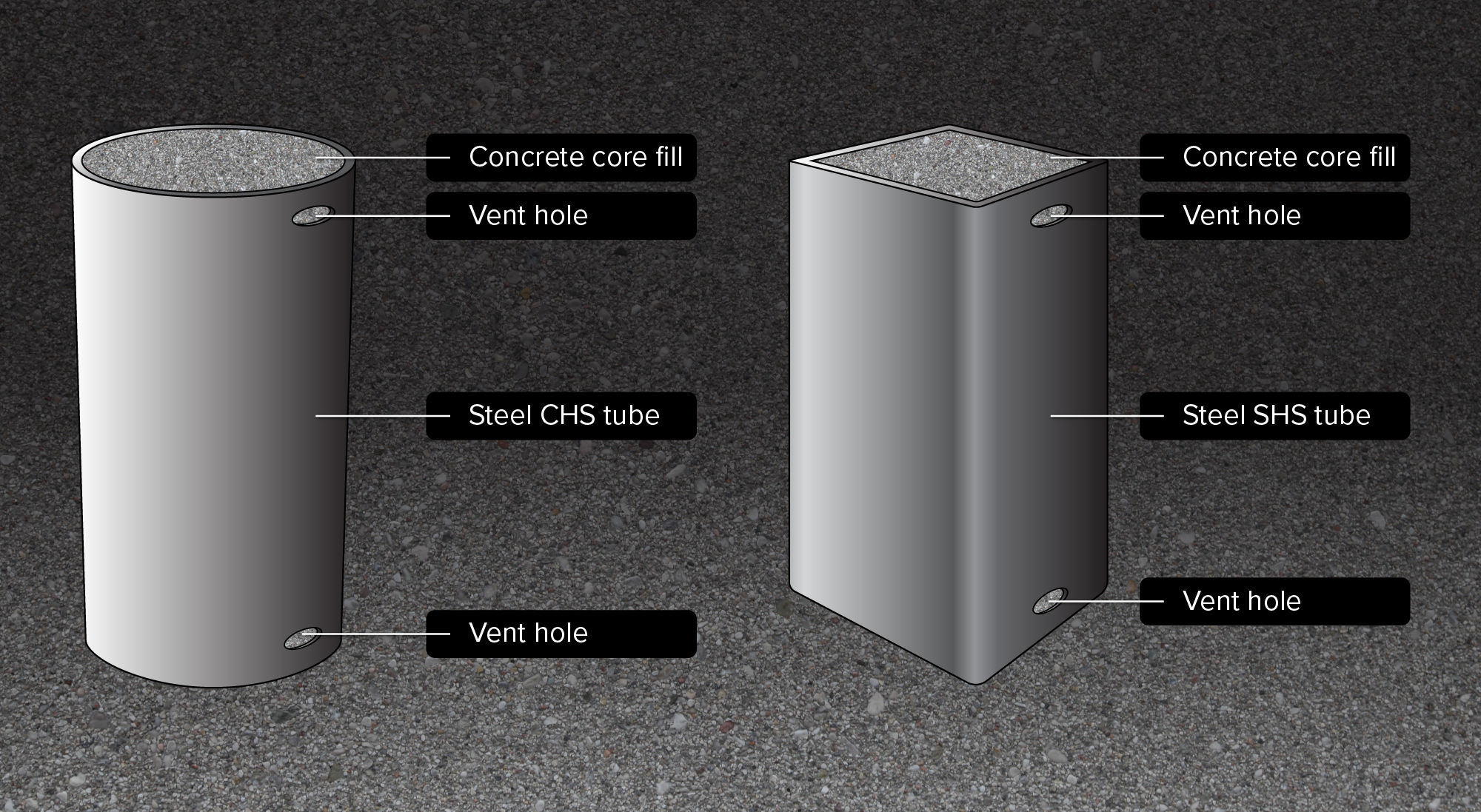
How core filling affects intumescent paint coatings
Core filling is a viable solution to fire-protect high Hp/A hollow section steel that is otherwise unable to achieve the desired FRL.